Снижение веса при производстве спутников
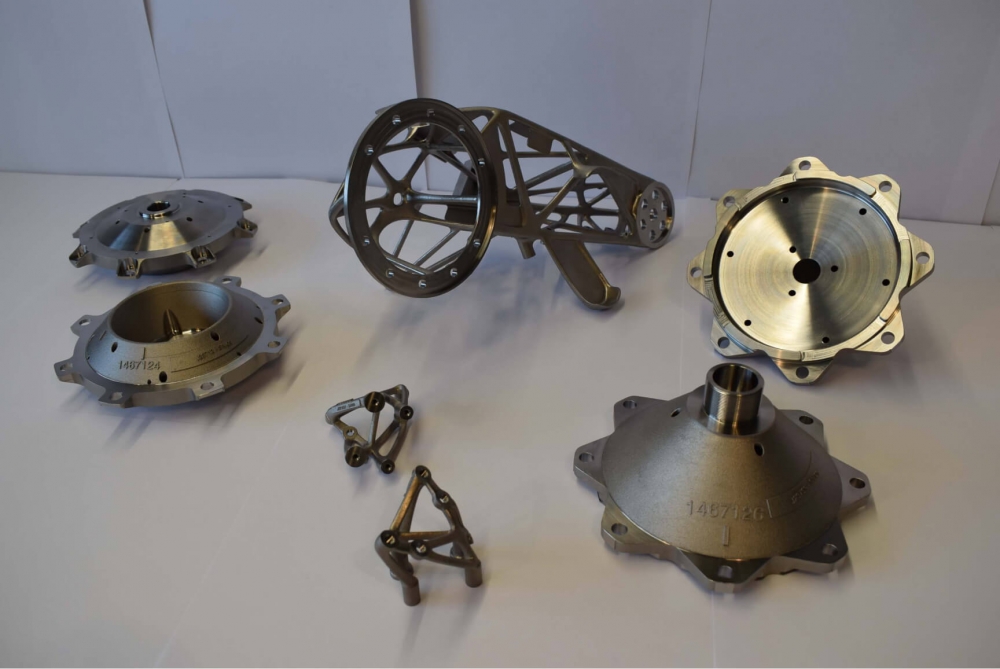
Спутники связи могут быть довольно большими по массе (и объему), например, первый Spacebus Neo (названный «Konnect») весил 3619 кг. Естественно, что при такой стоимости вывода вещей в космос каждый уменьшенный килограмм может привести к экономии затрат на запуск. Именно поэтому нам пригодятся 3д технологии, ведь с помощью таких инструментов, как AM и оптимизация топологии, возможно большее снижение массы при сохранении жесткости и прочности рассматриваемой детали.
Чтобы удовлетворить эти требования, компоненты были напечатаны из титанового материала LaserForm Ti6Al4V класса 23 на металлических принтерах DMP 3DSystems и собраны в конструкцию, которую вы видите ниже. Вся сборка образует 2-осевой подвес, который используется для позиционирования спутника на орбите с его системой электрического двигателя.
Наряду с топологической оптимизацией для механических сил, расчетное моделирование позволяет снизить накопление тепла и защитить функциональные компоненты от теплового повреждения. Согласно исследованиям, управление температурным режимом — это боль, когда нет жидкости, например, в космическом вакууме.
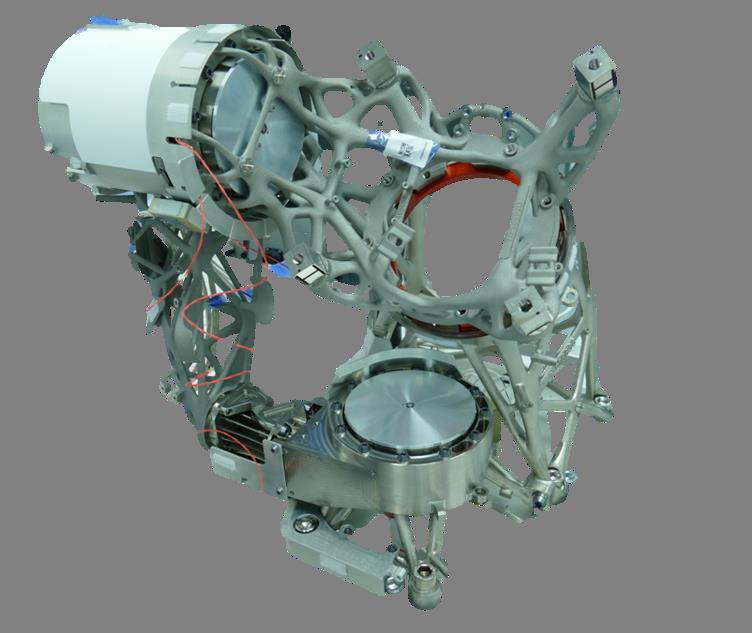
Конечно, вы не можете просто напечатать кучу металлических деталей и склеить их вместе, как кубики Lego, и надеяться, что полученная сборка будет квадратной, точной и соответствующей аэрокосмическим стандартам. Требовалось много постобработки и контроля качества, чтобы гарантировать, что детали были точными по размеру и подходили для стыковки.
С этой целью Thales Alenia Space разработала надежный производственный метод, включающий такие пост-процессы, как чистовая обработка с ЧПУ и 100% томографический контроль, чтобы гарантировать воспроизводимость продукта в контролируемой среде AS9100 (стандарты управления качеством ISO9001, разработанные для авиакосмической отрасли).
В результате они смогли изготовить конструктивный узел, который обеспечивал точность наведения 0.1 градуса, используя при этом повышенную эффективность двигателя за счет уменьшения массы топологически оптимизированных кронштейнов.
0 комментариев