10 000 деталей, напечатанных для серверов Oracle Labs
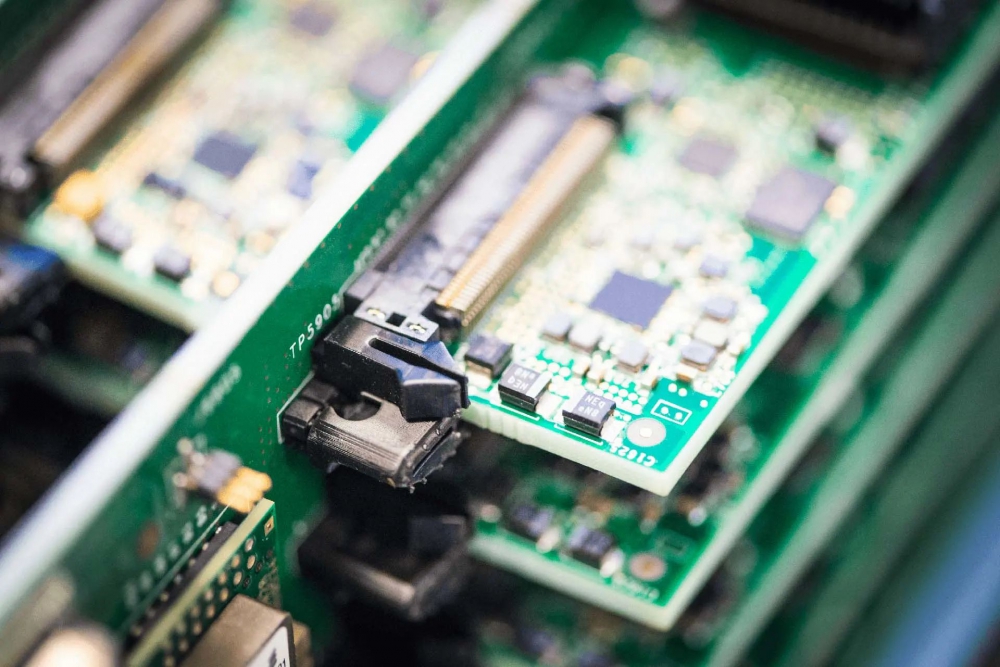
Oracle Labs — это научно-исследовательское подразделение многонациональной корпорации компьютерных технологий Oracle, которому потребовалось 10 000 деталей для выравнивания своих мини серверов в стойках, чтобы подключить их в более крупную сеть. Как обычно в таких случаях выполнить проект требовалось «ещё вчера», поэтому их выбор пал на 3д печать, позволившую развернуть производство в течение нескольких дней, а не месяцев.
Кстати, если вам нужна высокая вычислительная мощь, то рекомендую обратить внимание на серверы HPE ProLiant dL360. Эта энергоэффективная модель хорошо подходит для ограниченного пространства, обладает повышенной надежностью и легко администрируется через обычный веб-браузер.
Ну а мы продолжим. Сначала Oracle планировала разработать свой защелкивающийся кронштейн на основе литья под давлением, но этот метод оказался неэффективным при создании таких мелких деталей в требуемые сроки, а также не поддерживал быстрое прототипирование и несколько итераций дизайна. Именно тогда сотрудникам пришла в голову идея обратиться к ребятам из Carbon 3D.

Эта компания не новичок в 3D печати и уже давно использует несколько стандартных аддитивных технологий, но ни одна из них не предлагала решения, которое могло бы обеспечить высококачественные, повторяемые результаты в соответствии с требованиями Oracle для своих серверов. После долгих раздумий было предложено попробовать CLIP — процесс, который в 25-100 раз быстрее традиционной 3D печати.
Его особенностью является использование ультрафиолета, вызывающего полимеризацию, с кислородом, ингибирующим реакцию, а значит обычная 3D печать превращается в химический процесс. Управляя потоком кислорода, можно создать «мертвую зону» в десятки микрон в определенных областях бассейна со смолой, где фотополимеризация не происходит, а изделие получается как литое: гладкое снаружи и твердое внутри.
Но и это еще не все, ведь обычные SLA материалы были далеко не такими прочными, как требовалось, и не обеспечивали высокой точности повторяемых результатов. Пришлось снова взяться за ум и попробовать напечатать детали из смолы RPU 70 (жесткий полиуретан), которая по надежности и огнестойкости сопоставима с пластиком ABS. К счастью, все прошло как по маслу.

В итоге вместо нескольких месяцев результат был получен уже через несколько дней! Ведь компания не создавала каждую деталь по отдельности, а спроектировала ее так, чтобы она печаталась сразу целым кубом из кронштейнов. Учитывая, что CLIP является единственной аддитивной технологией, которая действительно обеспечивает непрерывный поток смолы во время процесса, что дает непревзойденное преимущество как в скорости, так и в прочности, подход был ограничен только тем, насколько далеко можно было выдвинуть ось Z!
«Oracle в восторге от сотрудничества с Carbon. Качество деталей оказалось намного лучше, чем у других технологий, которые мы пробовали ранее, а сам процесс изготовления сэкономил нам много времени».
Материал переведен 02.10.2024.
0 комментариев