Bugatti тестирует первый в мире 3D напечатанный титановый тормозной суппорт
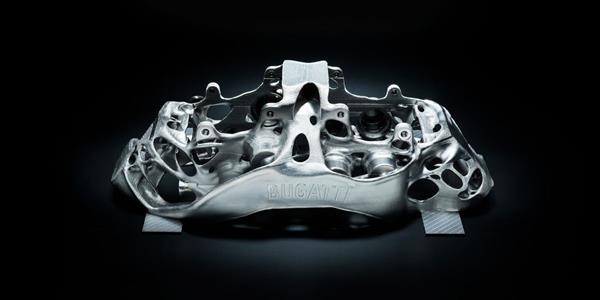
Всего через несколько лет почти все транспортные средства будут оснащаться напечатанными компонентами. Об этом свидетельствует растущее число компаний-производителей автомобилей, которые уже используют аддитивные методы или находятся на этапе исследований по включению 3D печати в свои цепочки поставок и сборочные линии. Французский производитель суперкаров Bugatti быстро переходит из одной группы в другую и недавно выпустил видеозапись, демонстрирующую жестокий стресс-тест напечатанного тормозного суппорта, предназначенного для установки на Chiron.
Bugatti Chiron оснащен 8-литровым 16-цилиндровым двигателем с четырьмя турбонагнетателями, который производит 1500 лошадиных сил и может развивать скорость до 407 км/ч. Важно, чтобы водители могли эффективно останавливаться на такой скорости, даже если они никогда не будут разгоняться до максимума. Поэтому Bugatti не отказывается от стресс-тестирования компонентов: они раскочегарили 3 кг титановый суппорт до скорости более 400 км в час и несколько раз останавливались, создавая температуру более 1000° С, которая, фактически, поджигала диск. В итоге суппорт остался целым, что говорит о многом, учитывая, что он весит примерно вдвое меньше, чем нынешние суппорты на Chiron.
Используя ту же технологию 3D печати, которая применялась для производства титановых колес, суппорт спекается из металлического порошка с помощью мощных лазеров. Процесс изготовления занимает 45 часов, а затем деталь подвергается химической и термической термообработке, что усиливает ее. Но хватит о технических аспектах. Наслаждайтесь фейерверком.
0 комментариев