Огромная металлическая аэрокосмическая деталь
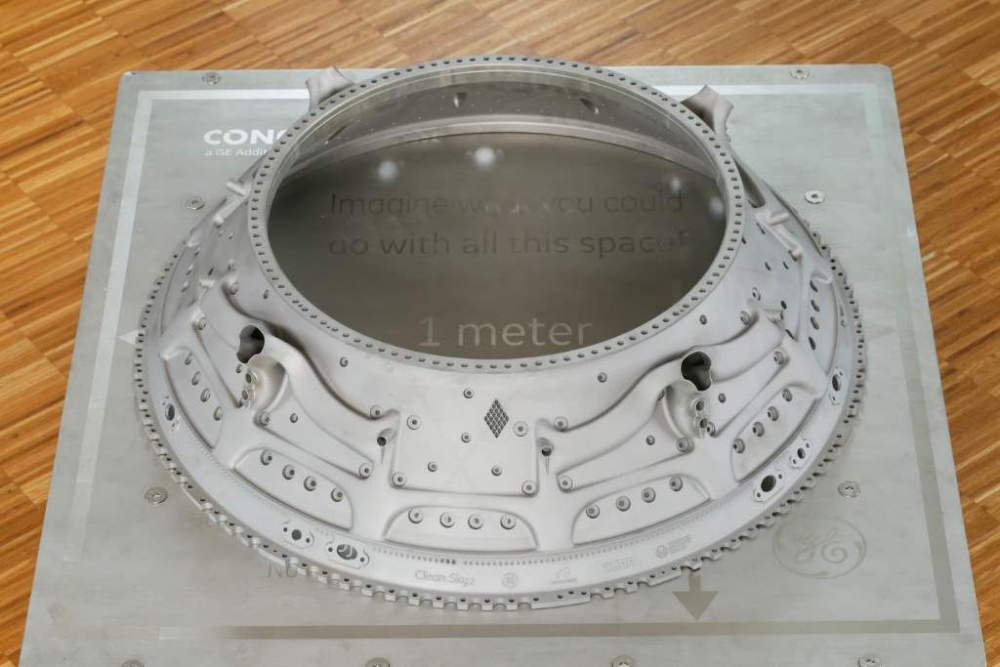
Консорциум из Гамбургского технологического университета (TUHH), Дрезденского технического института (TUD) и компании Autodesk в сотрудничестве с GE AAT Munich изготовил одну из самых больших металлических деталей для использования в аэрокосмической промышленности.
Корпус турбинного центра (TCF), созданный с помощью технологии Advanced Additive Integrated, был представлен после 6-летнего процесса разработки, включавшего тестирование, определение характеристик материалов, а также сборку и испытание самого компонента.
Изделие диаметром в 1 метр было напечатано из никелевого сплава 718 на системе GE Additive с помощью прямого лазерного плавления металла (DMLM).
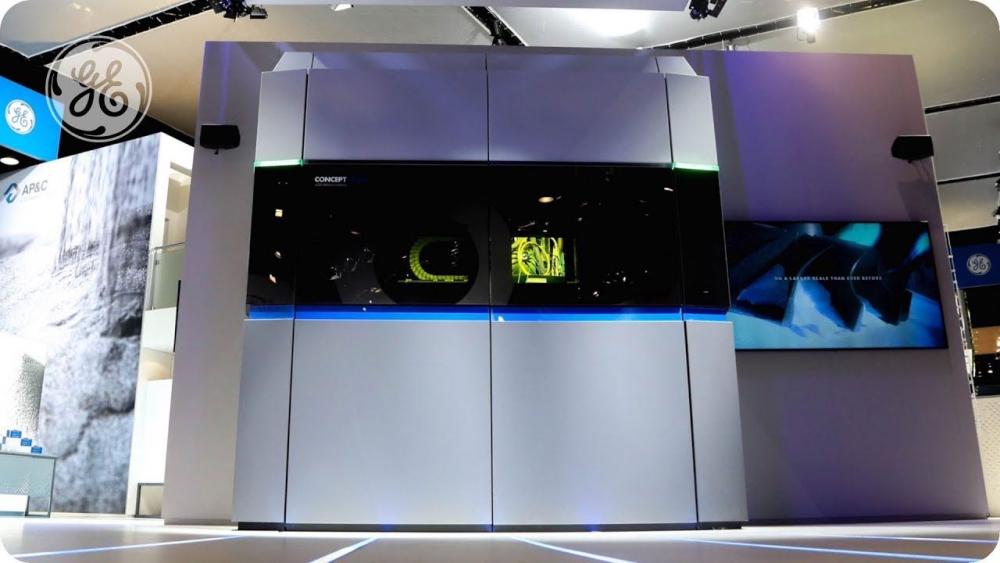
Использование печати вместо литья позволило сократить количество деталей со 150 отдельных частей до 1. К тому же, было показано, что масса и стоимость тоже уменьшились на 30%. Не стоит забывать и про время изготовления (без учета времени разработки, естественно) — оно сократилось с более чем девяти месяцев до всего двух с половиной.
Это решение появилось в ответ на запрос по проекту Clean Sky 2 — партнерству между Европейской комиссией и европейской авиационной промышленностью, которое координирует и финансирует исследовательскую деятельность для создания значительно более тихих экологически чистых самолетов. Снижение массы является важной частью достижения этих целей и АМ — перспективная технология, которая помогает им в этом.
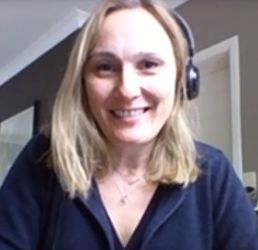
«Программа Clean Aviation, в соответствии с целью ЕС Green Deal по углеродной нейтральности к 2050 году, поддерживает запуск новых революционных продуктов для замены 75% действующего флота. Поэтому ускоренное время выхода на рынок и увеличение темпов производства будут иметь решающее значение для достижения этих амбициозных экологических целей».
Разработка велась поэтапно, на небольших участках и в меньших масштабах, постепенно повышая уровень готовности, пока процесс не стал достаточно зрелым.
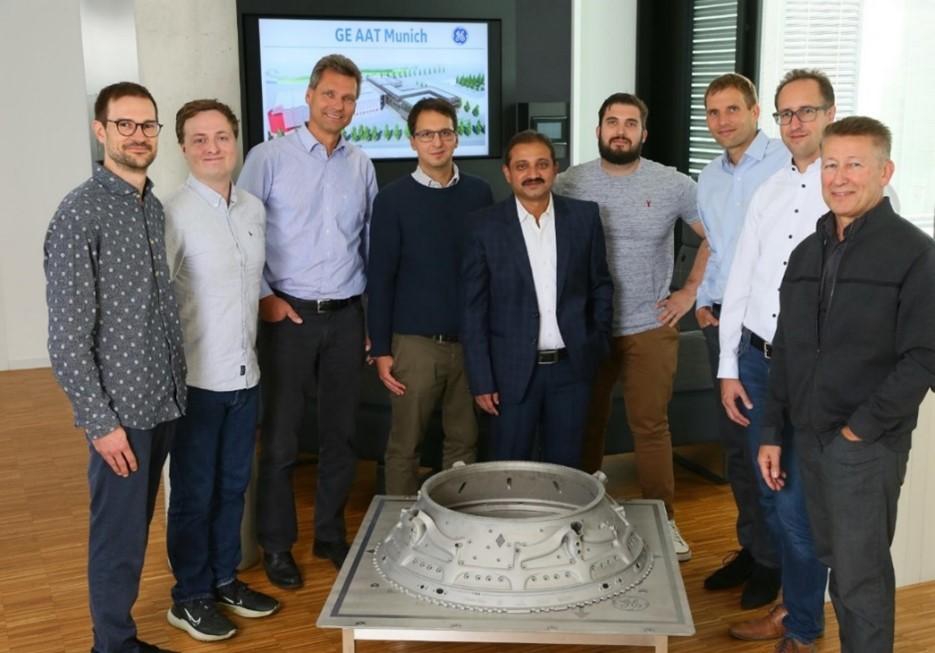
В конструкции использовано множество решений для снижения давления, тепловых градиентов и напряжения в компоненте. Фактическая работа по CAD, CFD и механическому моделированию была выполнена с помощью Autodesk и их различных программных пакетов.
Хорошей новостью является то, что подобный процесс применим не только для совершенно новых конструкций двигателей, но и может быть использован для существующих и устаревших моторов.
0 комментариев